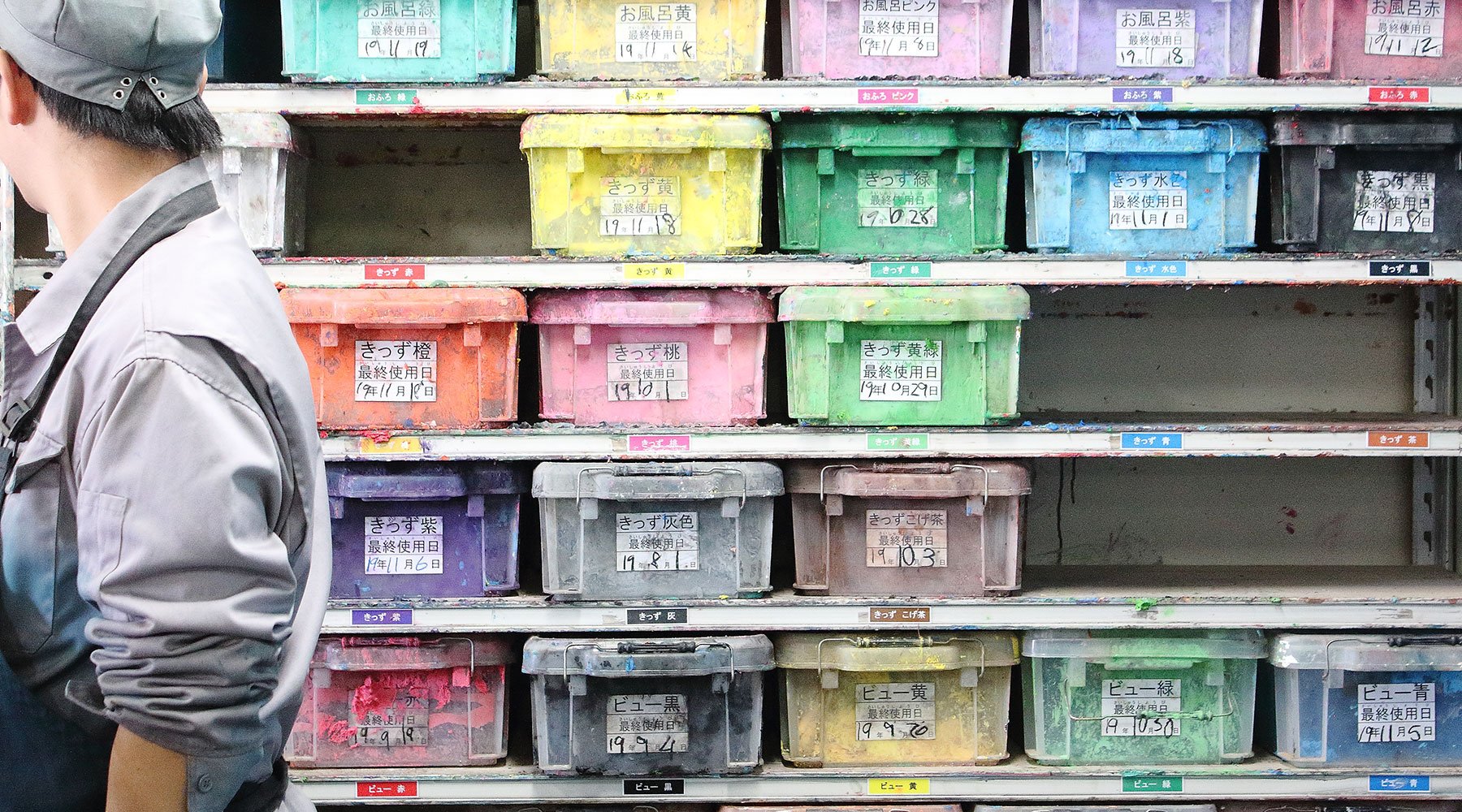
OUR STORY
OUR STORY
Kitpas was founded in 1937 as a manufacturer of regular chalks, and has been making quality art materials for over 80 years. We first began producing regular hard white chalks made from calcium carbonate, which soon became the preferred brand for many schools and businesses. In 1967, we expanded our production and built a factory in Hokkaido in the city of Bibai-shi, which translates to “Beautiful Shell City.”
It turns out that the city actually had massive waste piles of scallop shells from the food industry that were causing serious environmental issues. We wanted to find ways to reduce, reuse and recycle this material into our chalk production, as shells also contain calcium carbonate. With the help of the local government, we developed a patented process to recycle these seashell byproducts. The use of powdered shells had the additional benefit of making Kitpas Chalks stronger, smoother, and longer lasting! It’s no surprise that more than 60% of the chalks currently used by schools in Japan are Kitpas chalks.
As we continued our product development, we explored ideas for an innovative material that works on surfaces like paper, glass, mirrors and whiteboards. In 2005, we introduced our buttery-smooth, multi-surface, vibrant, water-soluble Kitpas Art Crayons, which are also exceptional in quality and non-toxic. They soon became the favorite choice of crayons for children and their parents, winning Japan’s prestigious “Stationery of the Year Award” in 2009. Starting in 2021, we have introduced rice bran wax as the primary ingredient of all of our art crayons to enhance both our safety and quality.
Today, Kitpas has evolved into Japan's leading manufacturer of innovative, eco-friendly art materials. We know you will love our products—let your creativity flow with Kitpas!
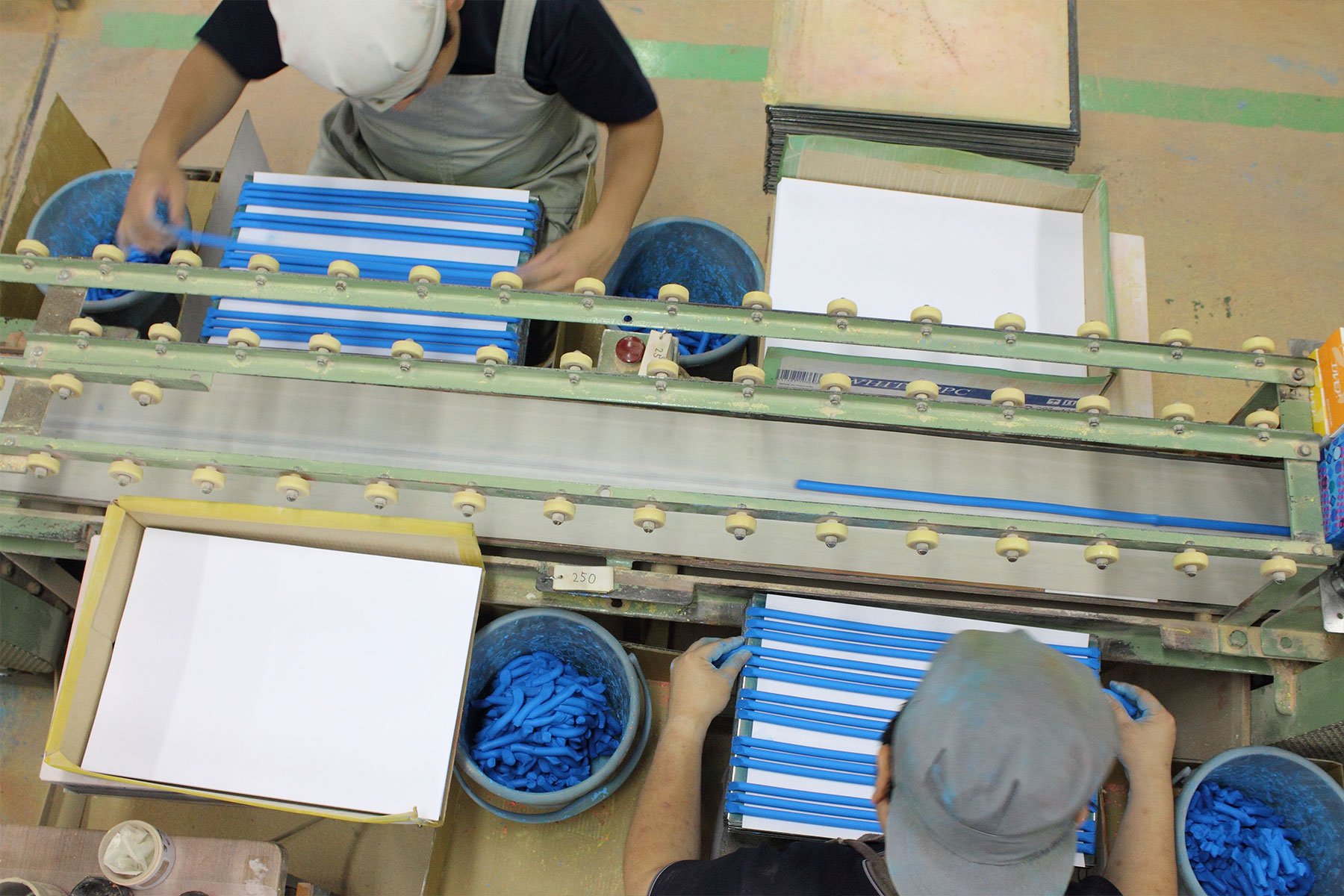
OUR VALUES
OUR VALUES AND COMMITMENT
Kitpas is guided by the philosophy that everyone, regardless of ability, can find happiness and satisfaction through their work. In 1960, we hired our first two employees with intellectual disabilities. Since then, we have adapted our manufacturing methods and work environment to suit the needs and abilities of all employees.
Currently about 70% of our employees have intellectual disabilities. We all work together in a cooperative space where hourglasses replace clocks, and measuring and testing devices have been designed specially for the needs of our employees.
We are committed to enhancing our customers’ creative experience while engaging in earth-friendly manufacturing and empowering people with disabilities. Our goal is to hire 100 employees with disabilities by the year 2030. We are proud of the positive impact we have on our employees, and hope that Kitpas will bring creativity and joy into the lives of our customers of all ages!
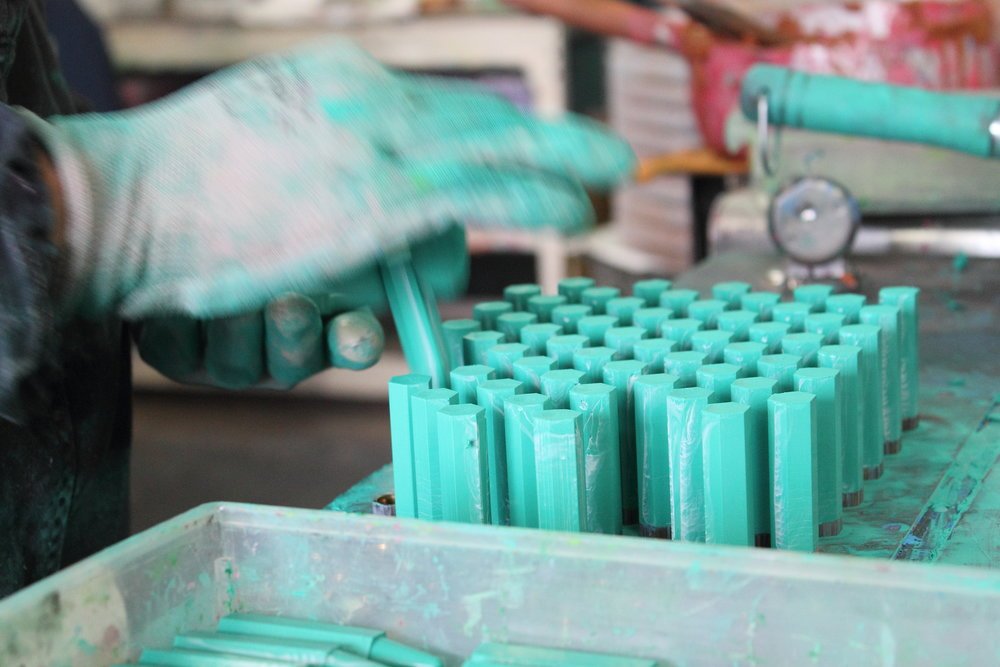
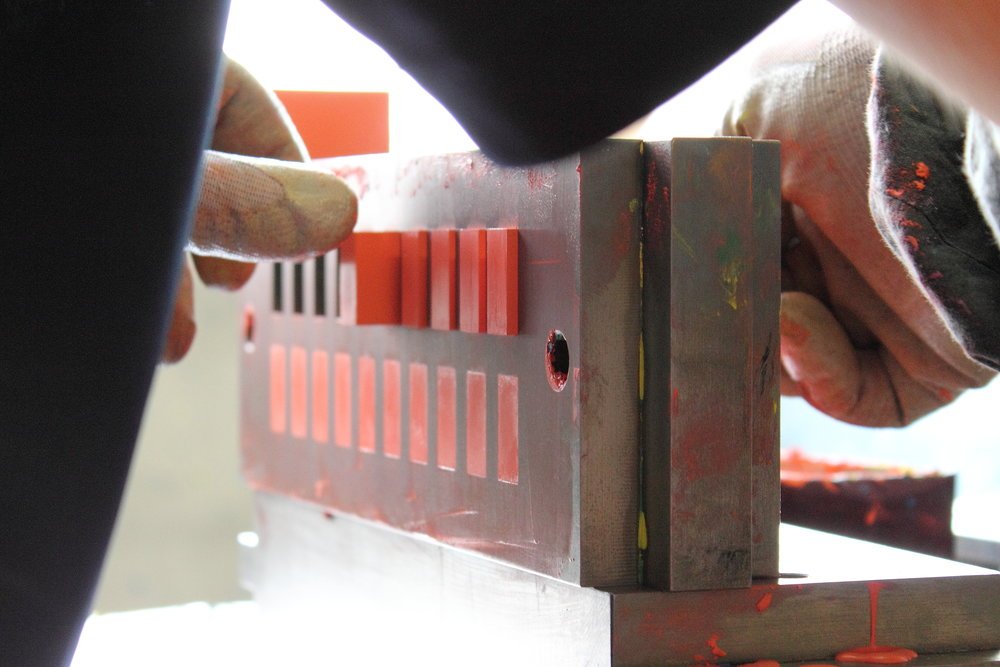
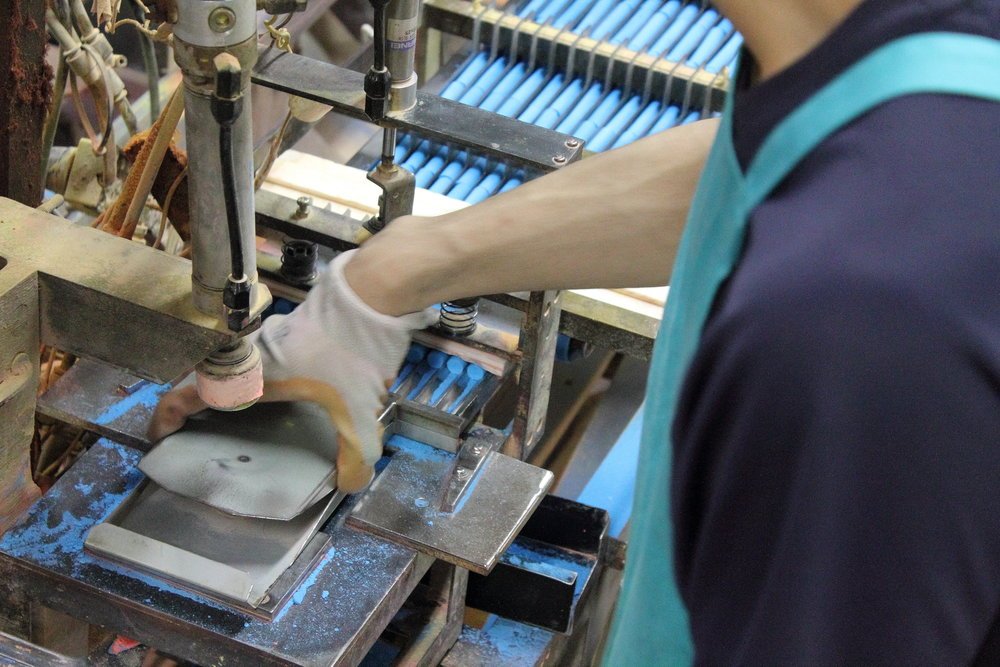
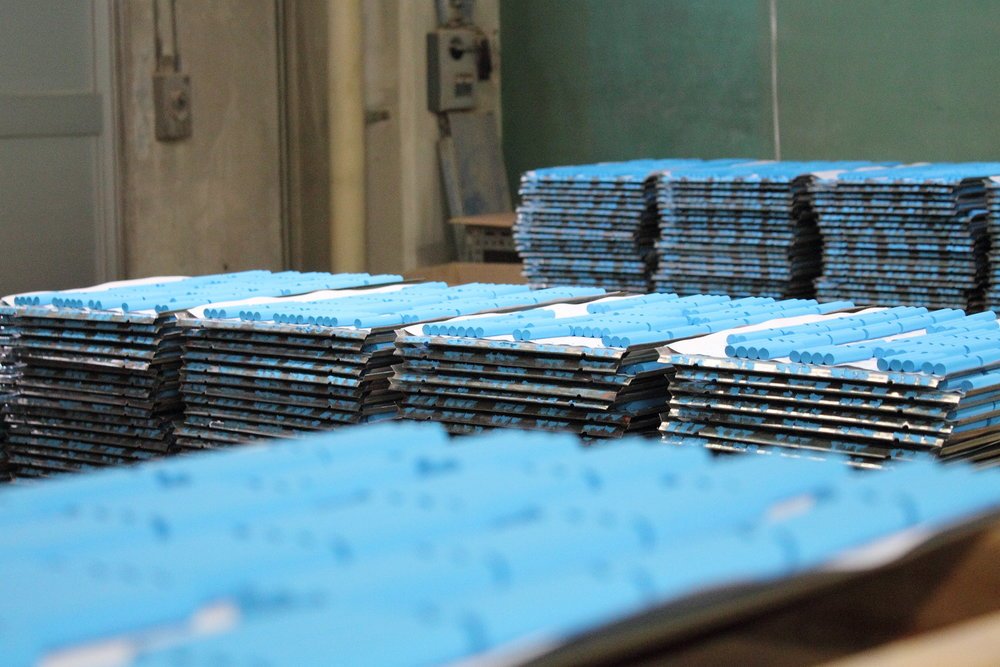
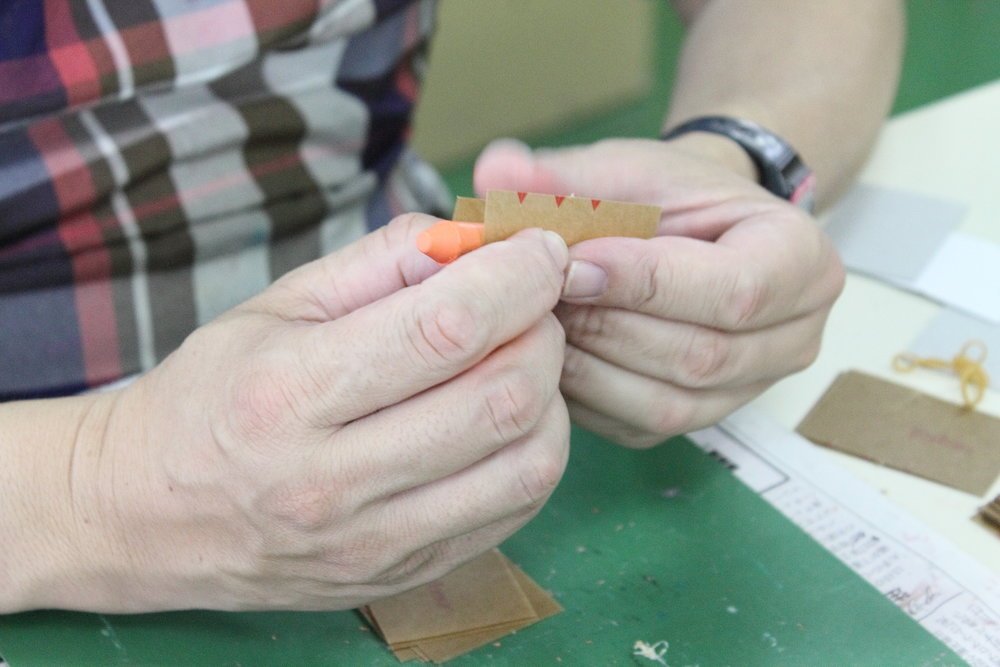
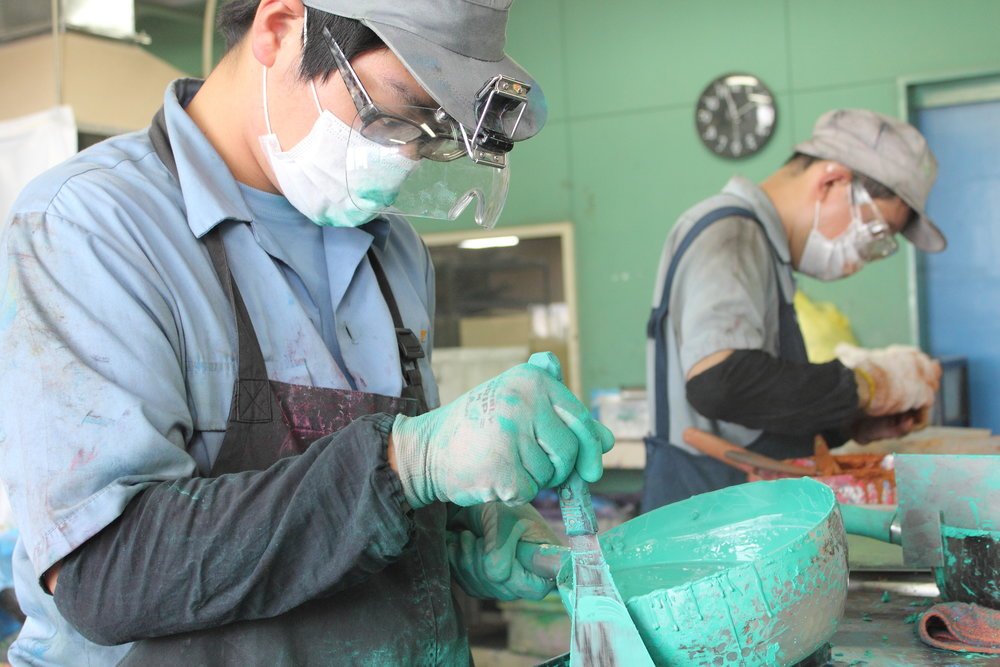
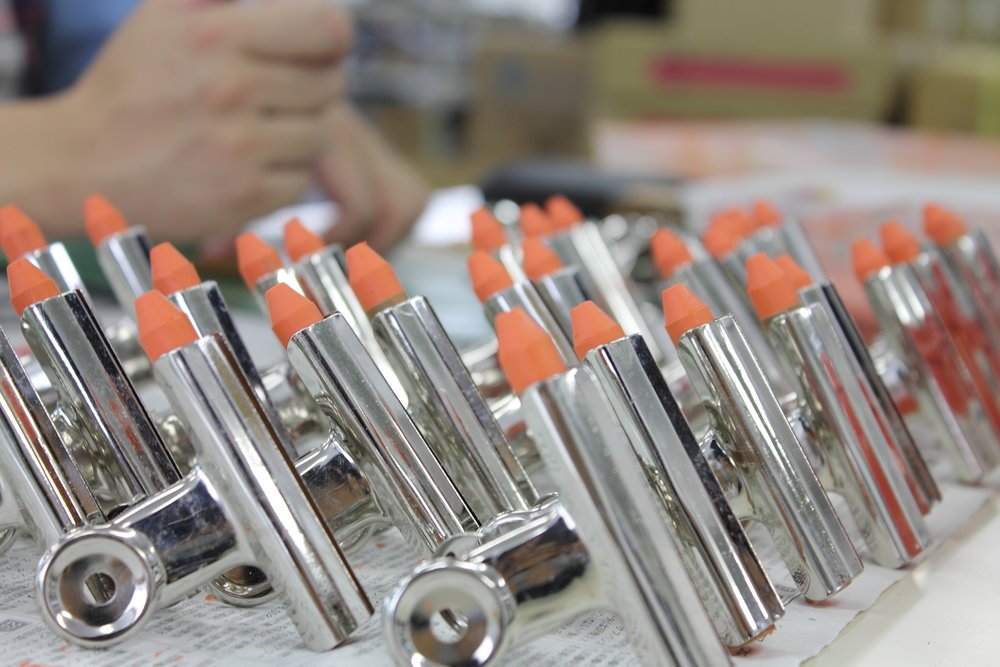
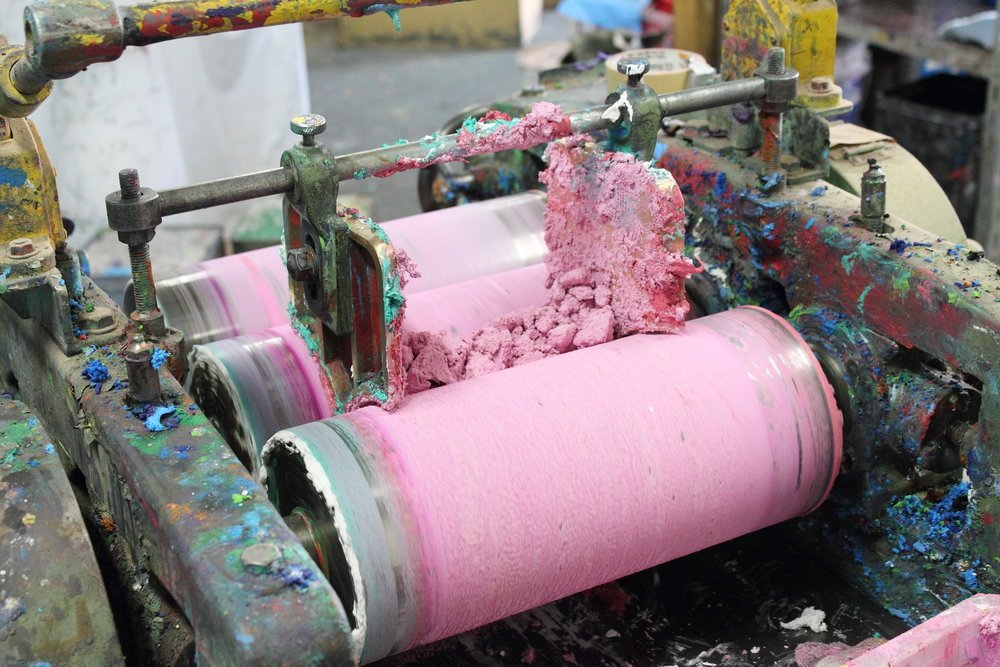
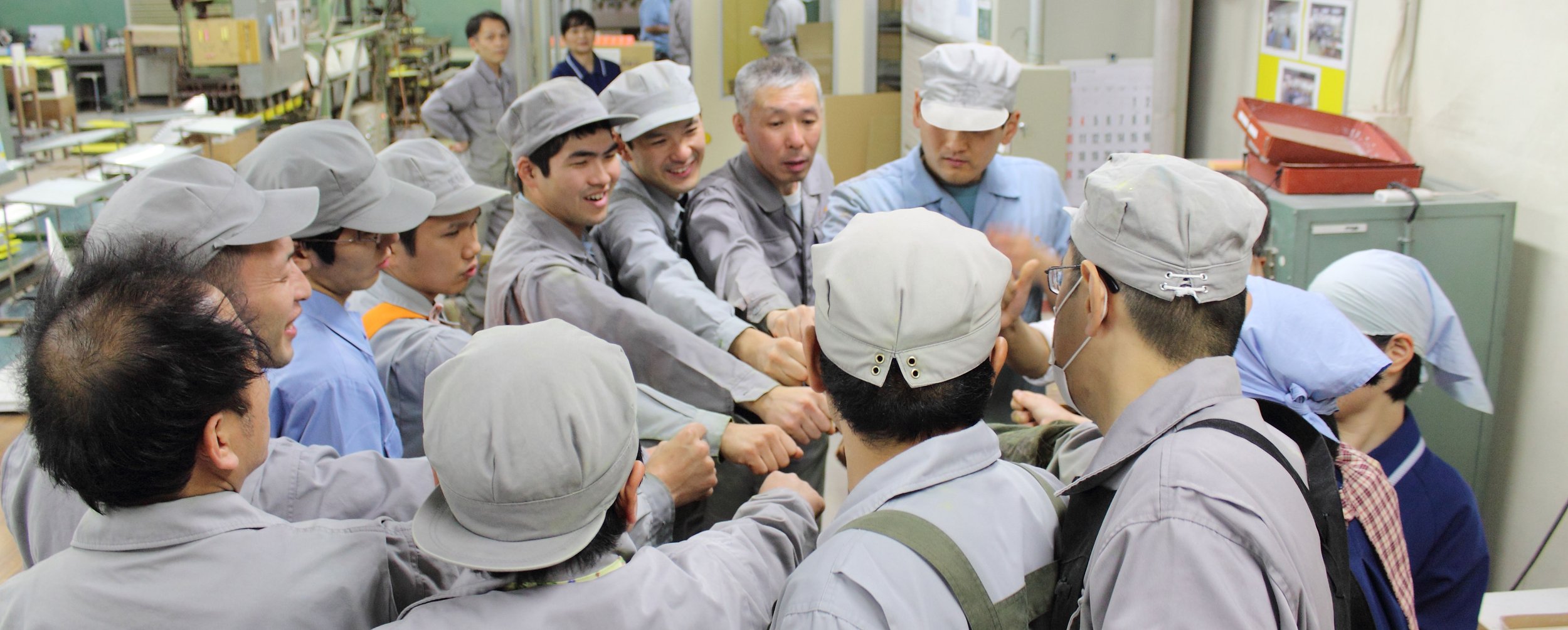
TEAM
-
Leader of kitpas Manufacturing Team
T. Y. (Joined in 1994)
He knows every single aspect of the kitpas production process––from molding to packaging––and leads the team at all times. He cares about others and always helps those in need of support. Everyone relies on him.
-
Member of kitpas Manufacturing Team
M. A. (Joined in 1994)
A master of folding kitpas package boxes which is one of the most complicated work and requires a lot of attention to details among all the manufacturing processes, she puts the final touches on her beautiful boxes.
“I would never say “I can't do it” even when it is challenging. Instead I will learn it and keep doing to the end! It is also my pleasure to teach other members what I have learned and to see they learn so I want to keep trying new things and learn a lot more."
-
Member of the Chalk Manufacturing Team
A. I. (Joined in 2010)
To pack 600 boxes of chalks (ie 4320 pieces) is my daily goal and I always do my work with that in mind. I feel happy when I do things for others, so I make shuriken (ninja star) for our "goal sheet" to use at our workplace with origami which is my hobby or give gifts to my colleagues. She is also active outside of her work.
-
Chief of the Chalk Manufacturing Team
A. T. (Joined in 2004)
I joined the company after graduating from high school and have been working for 17 years. I am in charge of the first process of chalk production, kneading work. It's fun to see how the white powder turns into chalk, but it is dangerous when you get too close, so I'm working pretty carefully.
-
Chief of the Chalk Manufacturing Team
M. Y. (Joined in 1997)
He is in charge of molding chalk that was extruded––his task is to pick up the soft chalk pieces as they come by on the conveyor belt and put them onto trays. It requires a lot of attention and concentration. He has an amazing ability to focus on things right away, so the job is perfect for him.
-
Member of kitpas and the Chalk Manufacturing Team
E. M. (Joined in 2004)
I am in charge of cutting chalks into sticks and packaging. I love beautiful things and I am most excited when I work on colorful Art Chalk.